The curious case of ethical carbon fibre
Carbon fibre has revolutionised mountain biking and cycling as a whole, but it also has a dark side
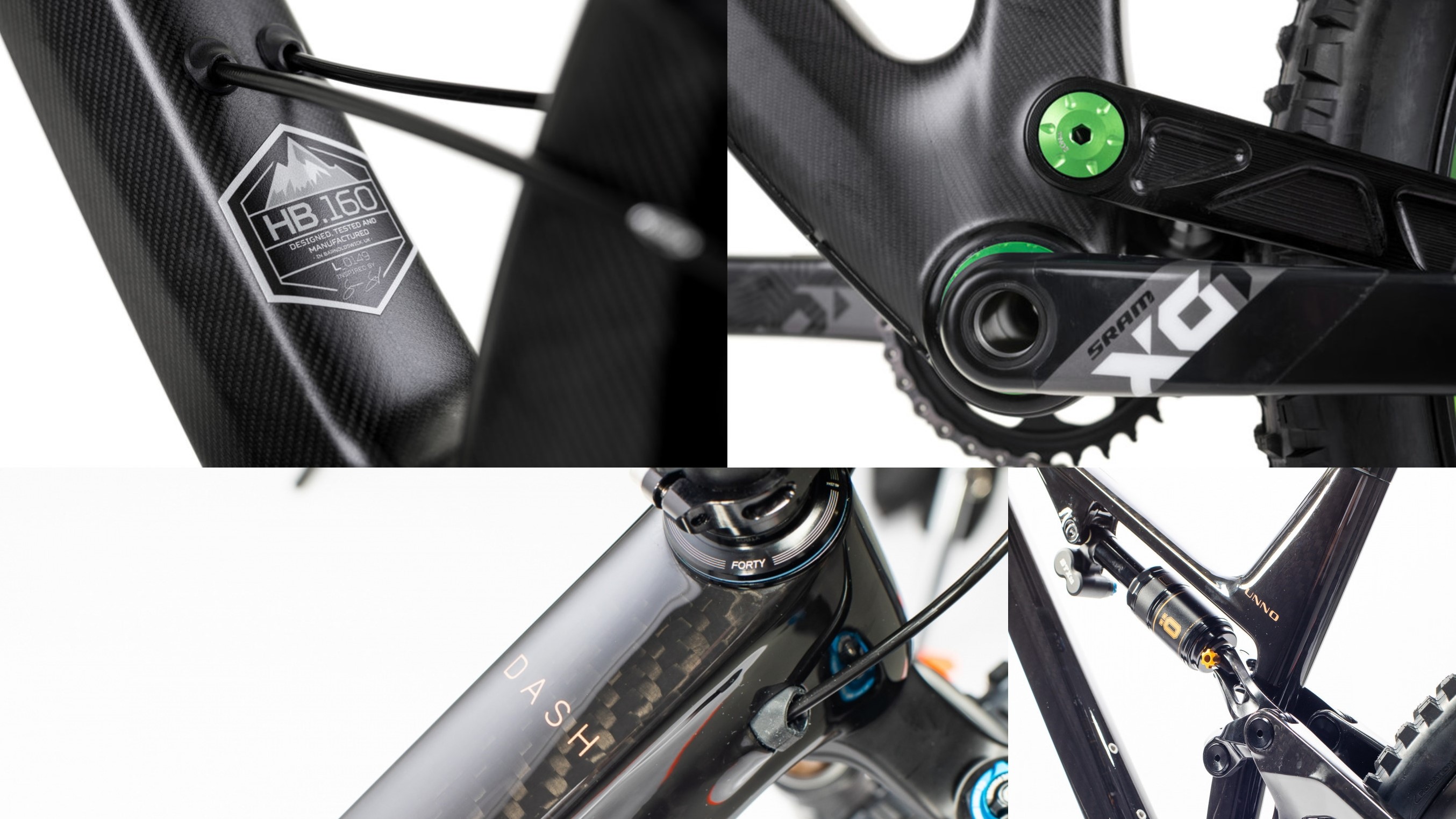
Two decades into the 21st century, there is no question that carbon fibre has changed the cycling industry more than any other design trend.
Classed as a miracle material by some, dark metal by others and an environmental issue by critics, carbon fibre is lighter and stronger than traditional cycling components, steel and alloy.
Engineers in the cycling industry always desire to make frames, wheels and other components lighter, without sacrificing strength. In mountain biking, with its technical terrain and high load-case impacts from rocks, roots, drop-offs and jumps, the strength-to-weight ratio becomes even more important.
A great benefit of carbon-fibre, beyond its strength-to-weight ratio, is how its fibre and epoxy structure enables engineers to fashion more complex shapes, with superior load distribution and vibration absorption.
Measured in terms of performance, carbon fibre has completely justified is cost premium and mass adoption by industry and riders alike. But there is a cost to carbon fibre. Something which is not readily seen when you admire that shiny new carbon frame or wheelset: where does it come from? And where does it end up?
Sourcing carbon responsibly
The global metalworking industry is centuries old, with an established supply chain and very mature manufacturing efficiencies. Sourcing steel or aluminium tube sets are easy and there is an abundance of talented artisans to weld them into bike frame shapes. Perhaps most importantly, metal is easily recyclable as the bicycle industry can dispose of its frames and components by accessing a much larger metal recycling system used by all industries.
Carbon fibre is a much newer material with evolving production methods. Sourcing quality carbon fibre is still a fraught process, especially for customers outside the defence, aviation and automotive realm.
The cycling industry is being challenged as more of its customers are asking where their carbon frames and components come from, and how they will be disposed of, at the end of their lifecycle. Environmental awareness is grading the purchase of carbon-fibre mountain bike frames and bits by considering sustainability instead of price or pure performance metrics such as weight.
Ethical carbon-fibre sourcing implies escalated cost. Working with carbon fibre is notably more involved than metal, requiring intensive labour intervention at many stages of the production process. Automation remains very limited in the production of composite frames and components, with up to 30 per cent of the base carbon-fibre fabric being wasted during initial trimming and cutting.
The bonding agent which cures carbon fibre into a set structure is mostly epoxy and those chemical formulations aren’t readily biodegradable. It also makes the finished carbon-fibre frame or component challenging to separate and recycle. Metal can easily be melted or recycled, while carbon fibre presents unique challenges.
And recycling it properly - too
Does the cycling industry have solutions in terms of ethical carbon? European composite mountain bike frame manufacturing has increased of late. In Barcelona, Unno is now doing the same for premium mountain bikes, at great cost, but to the highest possible labour and environmental standards. Hope has done much the same for the United Kingdom, with its HB130/160 dual-suspension frames.
Recycling solutions are increasing, with some offering real advantages, such as energy use. In an ideal world, ethically produced carbon will be recycled using only a tenth of the energy expended when it was originally produced.
The cost of some of these recycling processes is only a 5 per cent loss of strength in the constituent carbon fibres. This is the case with solvolysis, which uses pressure, water and organic solvents to sperate the carbon fibre and its epoxy.
In the future, more of these composite frames and components will hopefully detail their production sourcing and end-of-lifecycle planning, as part of the product narrative. This will allow mountain bikers who care equally about the environment and their riding enjoyment, to make truly make an informed decision about riding ethical carbon.
A lightweight and responsive carbon mountain bike frame or vibration-damping handlebar offers fantastic riding benefits. And if you feel confident in having made a sound purchase from an ethically sourcing company, you'll enjoy riding your carbon components even more.
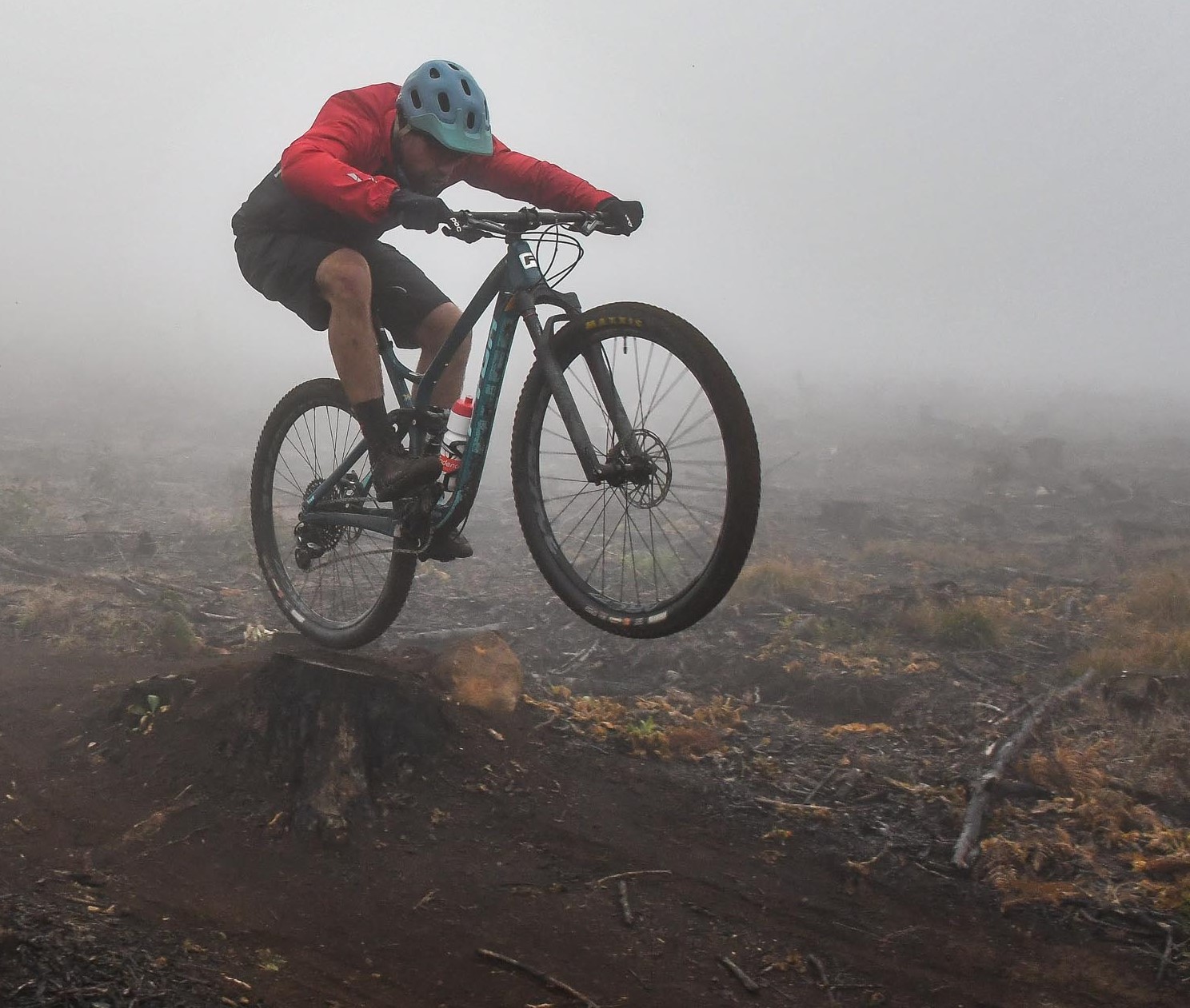
Lance Branquinho is a Namibian-born journalist who graduated to mountain biking after injuries curtailed his trail running. He has a weakness for British steel hardtails, especially those which only run a single gear. As well as Bike Perfect, Lance has written for MBR.com, Off-Road.cc and Cycling News.