Why are brakes still steel and not carbon-fibre?
Carbon brakes remain unworkable for mountain bikes
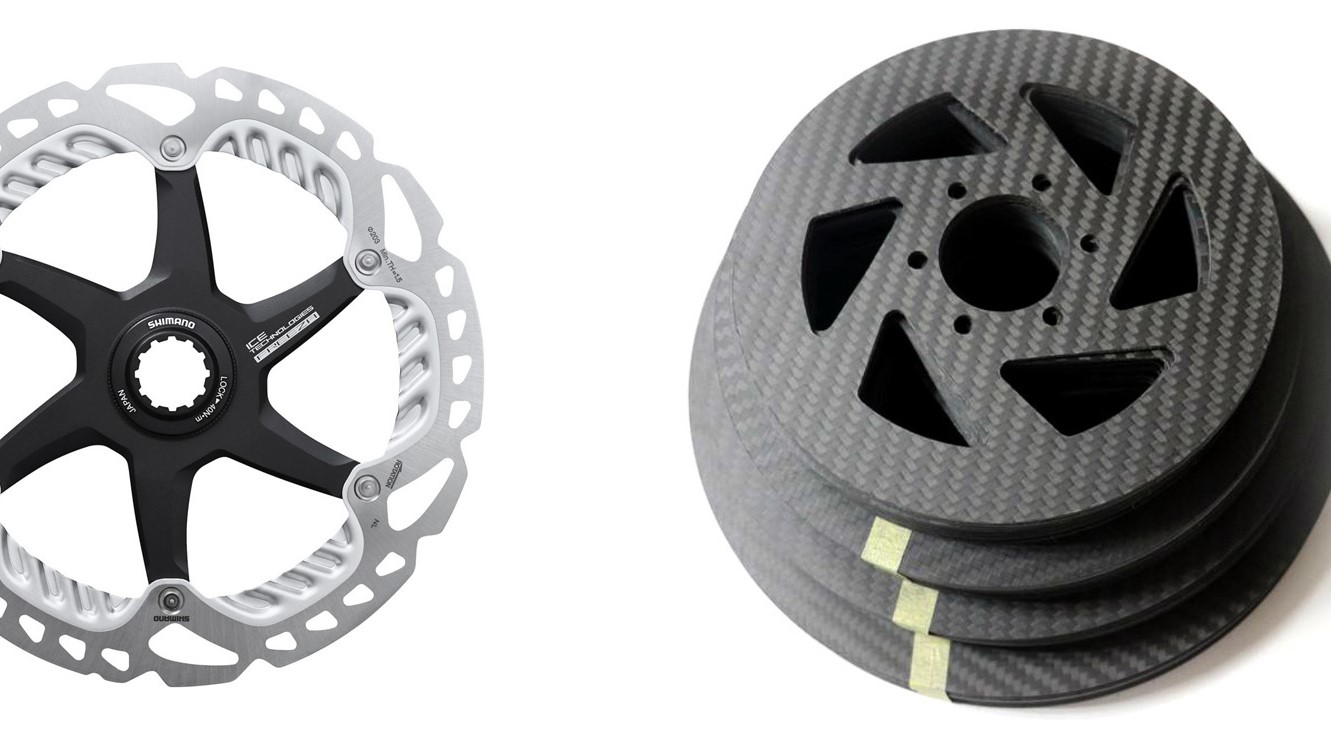
Brakes are strangely one of the mountain bike components which have resisted the conquest of carbon.
Although mountain bikers average slower speeds than road cyclists, we use our brakes a lot more intensely.
Trail features such as rock gardens, drop-offs and jumps require speed modulation, not to mention off-camber hairpin corners.
All these obstacles need to be approach at a respectful, and appropriate, speed. This means you feather and bite with the brake lever a great deal more on off-road singletrack than you’d ever do descending tarmac on your road bike.
Consequently, mountain bike brakes are very potent relative to their size. With the benefit of hydraulic actuation and large rotors you don’t require much squeezing force to enact rapid deceleration or even brake lock-up.
Hydraulic disc brakes work on a simple energy conversion principle where friction (between the caliper pads and rotor surface) is converted to heat, thereby extracting energy from rotational momentum at your front and rear axles – which slows you down. The better your brakes can manage that heat energy coefficient, the more powerful and predictably they’ll work.
Why steel?
Nearly all mountain bike brake rotors are steel. Despite carbon fibre being the vanguard mountain bike component material, it has not managed to displace metal as the brake structure of choice.
Carbon-fibre brakes should theoretically be much better than steel. When carbon-fibre is blended with a ceramic material, it has virtually unrivalled heat resistance – which means you could feather that brake lever down the longest and steepest descents without experience any loss in braking power.
Another aspect where carbon-fibre brakes would be superior to steel, is weight. Brake rotors are rotational components, so any mass saving is worth a notable gain in efficiency. The difference between a similarly sized steel and carbon-fibre brake rotor in mass is substantial, with the composite brake component weighing half of its metal counterpart.
If carbon-fibre brakes are lighter and theoretically work much better then steel, why can’t you buy them? Price is not a barrier to entry, as mountain bikers have always been willing to pay a huge premium for carbon-fibre components, especially in the early-adoption phase of product development.
Carbon compromises
The issues are brake rotor size and the thermal activation profile of carbon fibre.
Mountain bike brake calipers work on quite a narrow margin of pad movement and to ensure everything is packaged within tolerance, you require a rotor which is ideally no thicker than 2mm.
To shape steel into a disc profile where you can have a 140-, 160-, 180- or 203mm diameter shape that is between 1.5- and 2mm thin is achievable with a steel. Attempting the same structure in carbon fibre, is challenging.
Beyond the sizing issue carbon possesses surface properties, which when wet, make it an non-ideal brake component. Carbon brakes are also a victim of their own heat gradient. In an automobile, at high speeds, the energy conversion is so intense, that carbon brakes quickly warm to the correct operating temperature.
With mountain bikes, which turn far lower speeds and weigh a lot less than a car (even with a rider aboard), it is nearly impossible to generate the required spike in energy transfer. The result is that the temperatures to make a carbon brake disc system work simply aren’t practical in any mountain biking application.
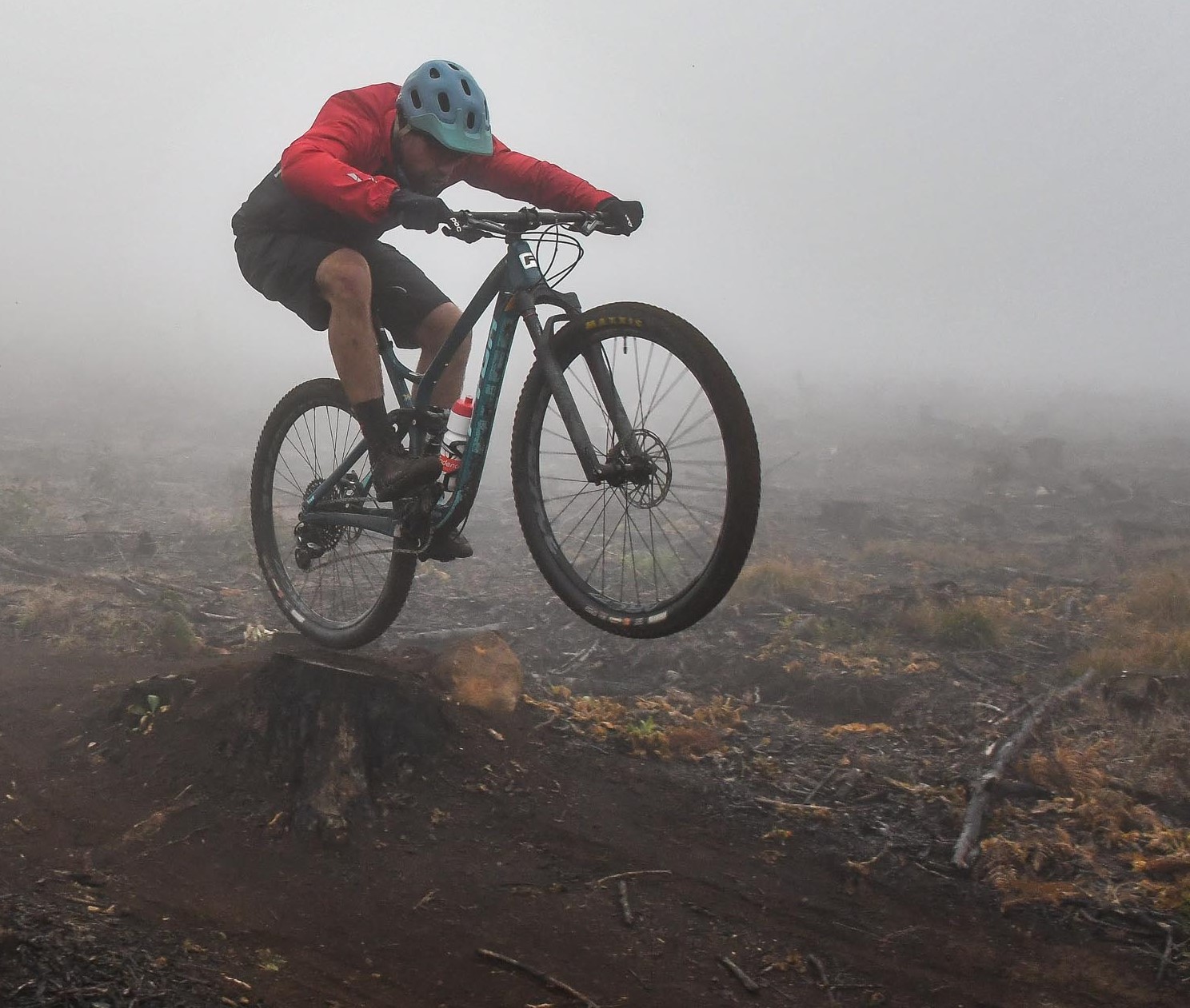
Lance Branquinho is a Namibian-born journalist who graduated to mountain biking after injuries curtailed his trail running. He has a weakness for British steel hardtails, especially those which only run a single gear. As well as Bike Perfect, Lance has written for MBR.com, Off-Road.cc and Cycling News.